1
2024.1.15
2016年9月12日
電炉設備・技術の変遷 ■共英製鋼特別顧問 深田信之氏 コスト減との戦い 枚方に直送システム 鉄スクラップの事前処理が重要
異形棒鋼メーカー最大手の共英製鋼で約半世紀にわたり、電炉製鋼・圧延設備の導入や操業に携わってきた深田信之氏。今年6月で取締役専務執行役員を退任し、特別顧問に就任した同氏に電炉設備・技術の変遷などについて、これまでのキャリアや時代背景とともに聞いた。
――入社当時について
「1960年に入社し、64年から佃工場(後の大阪工場、今年3月末に閉鎖)で普通造塊の生産に携わり、電炉操業のイロハを学んだ。当時は電炉でも酸素投入製鋼が行われ始め、シェルが開発したトロイダルバーナーといった現在の助燃バーナー(酸素と灯油燃焼)の初期設備が出てきた。この60年代の電炉創成期の中で、現場の仲間とともにバーナーや耐火煉瓦などより新しい設備等の導入に向けて取り組んだ。このことがその後の自身にとっての礎にもなった」
「さらに70年には佃工場に連続鋳造機(2ストランド・105角)を導入した。これは、住友重機がコンキャスト社と提携して製造し、関西の電炉メーカーでは国光製鋼に次いで2番目の導入となったものだが、既存の建屋に納めるという制約があったり、従来のトーチカットではなく、油圧シャーでビレットを切断するという新しいシステムにチャレンジしたりと苦労の連続だった。実はこの連続鋳造機の普及については、高炉メーカーより電炉メーカーの方が早かった。当時の高炉メーカーは連続鋳造に対して品質面などで懐疑的だったことに加えて、電炉メーカーが普通造塊では労働環境に問題を抱えていたこと、生産品種が鉄筋で高炉の高級材ではなかったことなどが普及スピードの差につながっており、これは米国でも同様だった」
――粗鋼生産の伸びに伴って、当時は電気炉の大型化が進む時代でもあった
「特に70年代初めから半ばにかけては小型電気炉が大型炉に切り変わっていく時代だった。また電気炉は元々特殊鋼を生産する設備として導入され発展してきたが、鉄スクラップ発生量の増加や原子力発電による電力の安定供給に伴う夜間電力使用でコスト面でも競争力がついたことなど、国内スクラップやエネルギー事情も普通鋼電炉の拡大につながったと考えている。当社でも71年にトランス容量の大きい大型炉を導入した。これは米国のW・E・シュワーベ氏が提唱したUHP(ウルトラハイパワー)理論に基づくもの。低電圧・大電流で生産性を上げるという操業理論で日本国内でも流行した。しかしながら、UHP理論を採用すると、その高エネルギーから電気炉の壁や蓋の寿命が短くなったため、その対策として水冷の炉壁・炉蓋が開発された。また、スラグラインの耐火煉瓦がもたないという問題もあったが、従来のマグネシア煉瓦に代わりカーボンを添加したマグカーボン煉瓦が開発され、これを採用した。さらに低電圧・大電流のUHP操業では炉壁の損耗や電極の消耗が大きいので、高電圧・低電流のロングアーク操業が日本で開発・導入された。とにかくこの時期は大型炉の生産性向上やコスト削減に試行錯誤の日々だった」
――この後米国での電炉工場立ち上げにも携わった
「共英製鋼が米国進出することを決めてオーバンスチール社を設立することになった際、74年から約3年間米国で勤務し、新しい40トン電気炉などの導入や立ち上げ、製鋼操業に携わった。当時の日本には普及していなかったフリッカー防止装置も米国では採用した。この頃オイルショックや当時のパートナーだった安宅産業が倒産するなど本社も苦労し、自分も米国から帰りの飛行機代があるのか心配になるような大変な状況だったが、いずれにせよ共英製鋼が日本の電炉メーカーとして初めて米国に進出するという、このフロンティアの先兵として現地に行ったことは自分の誇りであり、本当に多くのことを学んだ」
――米国での電炉工場の建設と操業立ち上げを終えて帰国した時期は、共英製鋼は非常に苦しい時期を迎えていた。
「76年に帰国して枚方工場へ赴任した当時は、とにかくコストダウンが至上命題。大阪工場時代の現場のみなが作業長・班長となっており、彼ら現場と一体となって『現場力』の力を発揮して難題をクリアしていった。この頃の製鋼は溶解期―酸化期―還元期に工程が分かれており、当時は還元期に精錬を行うのが一般的で、還元期にカーボン粉末を吹いて脱硫していたが、枚方工場ではその前の酸化期でもカーボン粉末を吹き込んで酸化スラグ中の鉄分を還元し、より歩留まりを上げる操業を徹底した。この操業技術開発がブラジルのゲルダウなど、海外で非常に評価されて技術指導を行う決め手にもなった」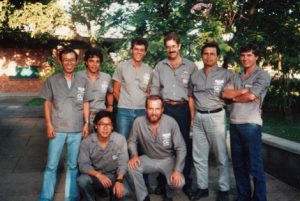
「また当時は生産効率を向上させるための設備導入が急速に進み、当時勤務していた枚方工場では電極原単位を下げるための電極水冷スプレー、スクラップ予熱装置のほか、酸素ガス発生装置を導入して酸素富加操業を開始し、さらにトランス容量アップやモールド電磁攪拌も相次いで採用していった。なかでも直接電極にスプレーで水をかける技術や電極接続装置などは枚方工場で独自開発した」
――和歌山共英製鋼(現日鉄住金スチール)を設立にも携わった
「小型のH形鋼の生産拠点として、当時の住金和歌山製鉄所内に設立した。年産30万トン程度であれば投資を抑えるために中古の30トン程度の電気炉を導入する計画もあったが、ちょうどこの年に東京製鉄さんが九州工場に直流電気炉を導入すると発表しており、『共英製鋼の技術は世界に誇るもので、和歌山でも直流電気炉にチャレンジしたい』と当時の会長(故高島浩一氏)、社長(高島成光相談役)を説得した。さらにLF(取鍋精錬炉)はメーカーに頼らず自社でつくり上げた。連続鋳造設備(CC)については休止していた和歌山製鉄所のブルームCCを活用することとなったが、共英製鋼に専門技術はなく、同所の現場から52名の方に応援に来て頂いた。当時、和歌山製鉄所の工場長でいらっしゃった友野さん(宏氏、新日鉄住金相談役)や製鋼部の皆さんには非常にお世話になった。また、92年には国内で初めて、電気炉で鉄スクラップと高炉溶銑を併用した電炉操業技術が確立できた。今ではミニ高炉と電気炉を組み合わせて鉄スクラップと溶銑を併用するこの製鋼法が中国、さらにベトナムで増えているようだ」
――90年代、そして2000年代とさらに電炉設備・操業技術の進化が続いていく
「例えば当社では92年に名古屋事業所の製鋼工場を更新する際に、日本で初めてスクラップの連続予熱・装入が可能なコンスチールシステムを採用した直流電気炉を立ち上げた。コンスチールは米国で開発されたばかりで、ノウハウもなかったものを当時の日本鋼管が設備の設計開発をした。また、夜間に特化した生産が主流となっており、この短い時間に出来る限り速く鋳込むため、高速モールドを大阪工場で開発して特許も取得した」
「2000年以降はダイオキシン対策や電炉操作室のオートメーション化、トランス更新などに取り組んできたが、何よりも大きな取組みとなったのが枚方工場での直送システムの導入で、エネルギー長官賞なども頂いた。さらにここ数年は使用電力のバラつきを抑えるためのリアクター更新、電力原単位の引き下げへ向けた電極サイズのアップなどのほか、各事業所でCO―JETバーナーの更新・導入で生産性・歩留まり向上を図った。また、廃ガスを分析して炉内燃焼する廃ガスコントロール、省電力のためにありとあらゆる熱源となる素材を投入するというケミカルエネルギーの有効活用、最適電力投入システムといった次世代に向けた操業への取り組み・ノウハウづくりを進めている」
――これまで電炉設備に携わる中で苦労したことは
「個人的には入社直後、小型電炉時代の佃工場で天井煉瓦の寿命が不安定だったことで非常に苦労した。当時、天井に使っていたレンガは珪石だった。珪石は軽くて日本でも多く取れるものの、採掘される山によって膨張・収縮など特性が違うためだ。大型電炉時代を迎えた後は先に述べたUHP操業時の炉壁損傷のほか、電極の折損などのトラブル、鉄スクラップ予熱による臭気対策、そしてDC炉の炉底電極の開発は大変苦労した」
――安定操業へ向けた重要な点は
「鉄スクラップから製鋼―圧延までの一連の工程にボトルネックがないことが理想的。ただ、設備導入・更新によって能力のアンバランスは生じるもので、必ずしもこれが悪いことではない。このアンバランスがあるからこそ、知恵やアイディアが生まれる。もちろん設備のメンテナンスと保守管理、オーバーホールによる弱点箇所の修復も重要だ」
――日本と海外電炉の違いについて
「海外、特に欧米では省人化が進んでいる。人件費が高く、安全管理に対して非常に厳しいためだ。また、普通鋼電炉は生産性・コストを中心に考えられており、100トン以上の大型炉が主流。電力供給源に余裕がある地域が多く、電力料金が安価なので日本の操業に比べて酸素やガスの使用量も少なく、海外電炉の電力原単位はおよそトン当たり400キロワット代となっている。また、電力料金が安い海外、特に水力発電が盛んなブラジルなどでは加熱炉に誘導炉を採用しているケースもある」
――今後求められる発展の方向性をどう考えるか
「電炉は鉄スクラップを再生する設備として最適だと考えており、CO2の排出量も少ない製鉄業ということを前提に、今後求められる課題は電気や化石燃料など投入エネルギーの最適化と環境設備の統合だ。特にスクラップや廃棄物を扱う以上、環境問題は避けて通れない。ダストや臭気、ダイオキシン、騒音などについてはこれまでに解決されてきているが、今後はさらに法令や規則などが厳しくなっていく可能性もある。また、ガスなど排出エネルギーの熱回収は高炉に比べてかなり遅れており、今後の課題の一つだ」
「製造品種の多様化・高度化に適応できる設備の合理化も必要になるだろう。同時に省人化・省力化へ向けたITも有力活用すべき。また、これら能率・効率・品質アップのためには、最終的には鉄スクラップの事前処理が重要となる。日本における鉄スクラップの事前処理レベルが進んでいるとは思えない。コンスチールやエコアークなどが試行される中、これらの設備の弱点を補うのに鉄スクラップの徹底した事前処理は不可欠。ニューコアやゲルダウなどが鉄スクラップ企業を買収しているのは価格面だけではなく、スクラップ部門の段階で製品の用途別に配合することが可能となるためではないだろうか」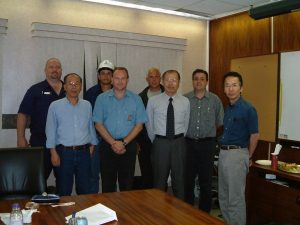
――深田さんが描く理想の電炉工場は
「非常に難しい質問だが、やはり操作室から全作業が操作できる、女性でも働けるような現場・炉前無人化工場が理想ではないか。特に日本では、女性が電炉の現場で働いているのは成分分析など一部業務にとどまっている。設備技術的には決められた鉄スクラップを投入すれば設計通りのエネルギーが計算されて出鋼し、成分調整と温度調整はLFで行い、さらにLFはCC上に設置して連続鋳造し、このビレットを直送圧延する。そして工場レイアウトは階段のように、電気炉は最も高い位置に置きそこからLF―CCへと下へ下へ向かう、立体的で高低差を活用したクレーンレスが理想的だ」
――最後に若い世代の技術者へメッセージを
「将来に向けた理想を描いて挑戦して欲しい。そして、その理想を実現するのに何が必要なのか、足らないのかを考えてほしい。また5年先、10年先に自分がどのような仕事をしたいかという希望や思いを、学歴やキャリアにとらわれず持ってチャレンジしてもらいたい」
▽深田信之(ふかだ・のぶゆき)氏=1941年生まれ。1960年入社後当時の佃工場を経て米国オーバンスチール社の立ち上げに従事。米国やブラジルなど世界各国で技術指導を行った。また、ベトナム南部製造拠点のビナ・キョウエイ・スチール社の電炉工場立ち上げに向け、ベトナム新ミル建設統括本部長として携わり、今年6月取締役専務執行役員を退任して特別顧問に就任した。
――入社当時について
「1960年に入社し、64年から佃工場(後の大阪工場、今年3月末に閉鎖)で普通造塊の生産に携わり、電炉操業のイロハを学んだ。当時は電炉でも酸素投入製鋼が行われ始め、シェルが開発したトロイダルバーナーといった現在の助燃バーナー(酸素と灯油燃焼)の初期設備が出てきた。この60年代の電炉創成期の中で、現場の仲間とともにバーナーや耐火煉瓦などより新しい設備等の導入に向けて取り組んだ。このことがその後の自身にとっての礎にもなった」
「さらに70年には佃工場に連続鋳造機(2ストランド・105角)を導入した。これは、住友重機がコンキャスト社と提携して製造し、関西の電炉メーカーでは国光製鋼に次いで2番目の導入となったものだが、既存の建屋に納めるという制約があったり、従来のトーチカットではなく、油圧シャーでビレットを切断するという新しいシステムにチャレンジしたりと苦労の連続だった。実はこの連続鋳造機の普及については、高炉メーカーより電炉メーカーの方が早かった。当時の高炉メーカーは連続鋳造に対して品質面などで懐疑的だったことに加えて、電炉メーカーが普通造塊では労働環境に問題を抱えていたこと、生産品種が鉄筋で高炉の高級材ではなかったことなどが普及スピードの差につながっており、これは米国でも同様だった」
――粗鋼生産の伸びに伴って、当時は電気炉の大型化が進む時代でもあった
「特に70年代初めから半ばにかけては小型電気炉が大型炉に切り変わっていく時代だった。また電気炉は元々特殊鋼を生産する設備として導入され発展してきたが、鉄スクラップ発生量の増加や原子力発電による電力の安定供給に伴う夜間電力使用でコスト面でも競争力がついたことなど、国内スクラップやエネルギー事情も普通鋼電炉の拡大につながったと考えている。当社でも71年にトランス容量の大きい大型炉を導入した。これは米国のW・E・シュワーベ氏が提唱したUHP(ウルトラハイパワー)理論に基づくもの。低電圧・大電流で生産性を上げるという操業理論で日本国内でも流行した。しかしながら、UHP理論を採用すると、その高エネルギーから電気炉の壁や蓋の寿命が短くなったため、その対策として水冷の炉壁・炉蓋が開発された。また、スラグラインの耐火煉瓦がもたないという問題もあったが、従来のマグネシア煉瓦に代わりカーボンを添加したマグカーボン煉瓦が開発され、これを採用した。さらに低電圧・大電流のUHP操業では炉壁の損耗や電極の消耗が大きいので、高電圧・低電流のロングアーク操業が日本で開発・導入された。とにかくこの時期は大型炉の生産性向上やコスト削減に試行錯誤の日々だった」
――この後米国での電炉工場立ち上げにも携わった
「共英製鋼が米国進出することを決めてオーバンスチール社を設立することになった際、74年から約3年間米国で勤務し、新しい40トン電気炉などの導入や立ち上げ、製鋼操業に携わった。当時の日本には普及していなかったフリッカー防止装置も米国では採用した。この頃オイルショックや当時のパートナーだった安宅産業が倒産するなど本社も苦労し、自分も米国から帰りの飛行機代があるのか心配になるような大変な状況だったが、いずれにせよ共英製鋼が日本の電炉メーカーとして初めて米国に進出するという、このフロンティアの先兵として現地に行ったことは自分の誇りであり、本当に多くのことを学んだ」
――米国での電炉工場の建設と操業立ち上げを終えて帰国した時期は、共英製鋼は非常に苦しい時期を迎えていた。
「76年に帰国して枚方工場へ赴任した当時は、とにかくコストダウンが至上命題。大阪工場時代の現場のみなが作業長・班長となっており、彼ら現場と一体となって『現場力』の力を発揮して難題をクリアしていった。この頃の製鋼は溶解期―酸化期―還元期に工程が分かれており、当時は還元期に精錬を行うのが一般的で、還元期にカーボン粉末を吹いて脱硫していたが、枚方工場ではその前の酸化期でもカーボン粉末を吹き込んで酸化スラグ中の鉄分を還元し、より歩留まりを上げる操業を徹底した。この操業技術開発がブラジルのゲルダウなど、海外で非常に評価されて技術指導を行う決め手にもなった」
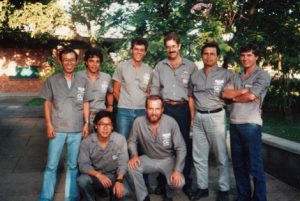
ゲルダオ アセノルテ(ブラジル・レシーフェ)
「また当時は生産効率を向上させるための設備導入が急速に進み、当時勤務していた枚方工場では電極原単位を下げるための電極水冷スプレー、スクラップ予熱装置のほか、酸素ガス発生装置を導入して酸素富加操業を開始し、さらにトランス容量アップやモールド電磁攪拌も相次いで採用していった。なかでも直接電極にスプレーで水をかける技術や電極接続装置などは枚方工場で独自開発した」
――和歌山共英製鋼(現日鉄住金スチール)を設立にも携わった
「小型のH形鋼の生産拠点として、当時の住金和歌山製鉄所内に設立した。年産30万トン程度であれば投資を抑えるために中古の30トン程度の電気炉を導入する計画もあったが、ちょうどこの年に東京製鉄さんが九州工場に直流電気炉を導入すると発表しており、『共英製鋼の技術は世界に誇るもので、和歌山でも直流電気炉にチャレンジしたい』と当時の会長(故高島浩一氏)、社長(高島成光相談役)を説得した。さらにLF(取鍋精錬炉)はメーカーに頼らず自社でつくり上げた。連続鋳造設備(CC)については休止していた和歌山製鉄所のブルームCCを活用することとなったが、共英製鋼に専門技術はなく、同所の現場から52名の方に応援に来て頂いた。当時、和歌山製鉄所の工場長でいらっしゃった友野さん(宏氏、新日鉄住金相談役)や製鋼部の皆さんには非常にお世話になった。また、92年には国内で初めて、電気炉で鉄スクラップと高炉溶銑を併用した電炉操業技術が確立できた。今ではミニ高炉と電気炉を組み合わせて鉄スクラップと溶銑を併用するこの製鋼法が中国、さらにベトナムで増えているようだ」
――90年代、そして2000年代とさらに電炉設備・操業技術の進化が続いていく
「例えば当社では92年に名古屋事業所の製鋼工場を更新する際に、日本で初めてスクラップの連続予熱・装入が可能なコンスチールシステムを採用した直流電気炉を立ち上げた。コンスチールは米国で開発されたばかりで、ノウハウもなかったものを当時の日本鋼管が設備の設計開発をした。また、夜間に特化した生産が主流となっており、この短い時間に出来る限り速く鋳込むため、高速モールドを大阪工場で開発して特許も取得した」
「2000年以降はダイオキシン対策や電炉操作室のオートメーション化、トランス更新などに取り組んできたが、何よりも大きな取組みとなったのが枚方工場での直送システムの導入で、エネルギー長官賞なども頂いた。さらにここ数年は使用電力のバラつきを抑えるためのリアクター更新、電力原単位の引き下げへ向けた電極サイズのアップなどのほか、各事業所でCO―JETバーナーの更新・導入で生産性・歩留まり向上を図った。また、廃ガスを分析して炉内燃焼する廃ガスコントロール、省電力のためにありとあらゆる熱源となる素材を投入するというケミカルエネルギーの有効活用、最適電力投入システムといった次世代に向けた操業への取り組み・ノウハウづくりを進めている」
――これまで電炉設備に携わる中で苦労したことは
「個人的には入社直後、小型電炉時代の佃工場で天井煉瓦の寿命が不安定だったことで非常に苦労した。当時、天井に使っていたレンガは珪石だった。珪石は軽くて日本でも多く取れるものの、採掘される山によって膨張・収縮など特性が違うためだ。大型電炉時代を迎えた後は先に述べたUHP操業時の炉壁損傷のほか、電極の折損などのトラブル、鉄スクラップ予熱による臭気対策、そしてDC炉の炉底電極の開発は大変苦労した」
――安定操業へ向けた重要な点は
「鉄スクラップから製鋼―圧延までの一連の工程にボトルネックがないことが理想的。ただ、設備導入・更新によって能力のアンバランスは生じるもので、必ずしもこれが悪いことではない。このアンバランスがあるからこそ、知恵やアイディアが生まれる。もちろん設備のメンテナンスと保守管理、オーバーホールによる弱点箇所の修復も重要だ」
――日本と海外電炉の違いについて
「海外、特に欧米では省人化が進んでいる。人件費が高く、安全管理に対して非常に厳しいためだ。また、普通鋼電炉は生産性・コストを中心に考えられており、100トン以上の大型炉が主流。電力供給源に余裕がある地域が多く、電力料金が安価なので日本の操業に比べて酸素やガスの使用量も少なく、海外電炉の電力原単位はおよそトン当たり400キロワット代となっている。また、電力料金が安い海外、特に水力発電が盛んなブラジルなどでは加熱炉に誘導炉を採用しているケースもある」
――今後求められる発展の方向性をどう考えるか
「電炉は鉄スクラップを再生する設備として最適だと考えており、CO2の排出量も少ない製鉄業ということを前提に、今後求められる課題は電気や化石燃料など投入エネルギーの最適化と環境設備の統合だ。特にスクラップや廃棄物を扱う以上、環境問題は避けて通れない。ダストや臭気、ダイオキシン、騒音などについてはこれまでに解決されてきているが、今後はさらに法令や規則などが厳しくなっていく可能性もある。また、ガスなど排出エネルギーの熱回収は高炉に比べてかなり遅れており、今後の課題の一つだ」
「製造品種の多様化・高度化に適応できる設備の合理化も必要になるだろう。同時に省人化・省力化へ向けたITも有力活用すべき。また、これら能率・効率・品質アップのためには、最終的には鉄スクラップの事前処理が重要となる。日本における鉄スクラップの事前処理レベルが進んでいるとは思えない。コンスチールやエコアークなどが試行される中、これらの設備の弱点を補うのに鉄スクラップの徹底した事前処理は不可欠。ニューコアやゲルダウなどが鉄スクラップ企業を買収しているのは価格面だけではなく、スクラップ部門の段階で製品の用途別に配合することが可能となるためではないだろうか」
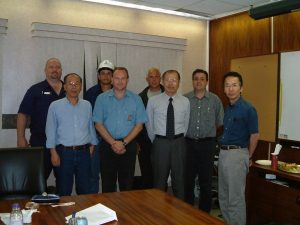
ゲルダオ Whitby (カナダ)
――深田さんが描く理想の電炉工場は
「非常に難しい質問だが、やはり操作室から全作業が操作できる、女性でも働けるような現場・炉前無人化工場が理想ではないか。特に日本では、女性が電炉の現場で働いているのは成分分析など一部業務にとどまっている。設備技術的には決められた鉄スクラップを投入すれば設計通りのエネルギーが計算されて出鋼し、成分調整と温度調整はLFで行い、さらにLFはCC上に設置して連続鋳造し、このビレットを直送圧延する。そして工場レイアウトは階段のように、電気炉は最も高い位置に置きそこからLF―CCへと下へ下へ向かう、立体的で高低差を活用したクレーンレスが理想的だ」
――最後に若い世代の技術者へメッセージを
「将来に向けた理想を描いて挑戦して欲しい。そして、その理想を実現するのに何が必要なのか、足らないのかを考えてほしい。また5年先、10年先に自分がどのような仕事をしたいかという希望や思いを、学歴やキャリアにとらわれず持ってチャレンジしてもらいたい」
▽深田信之(ふかだ・のぶゆき)氏=1941年生まれ。1960年入社後当時の佃工場を経て米国オーバンスチール社の立ち上げに従事。米国やブラジルなど世界各国で技術指導を行った。また、ベトナム南部製造拠点のビナ・キョウエイ・スチール社の電炉工場立ち上げに向け、ベトナム新ミル建設統括本部長として携わり、今年6月取締役専務執行役員を退任して特別顧問に就任した。

スポンサーリンク