1
2024.1.15
2020年3月29日
産業新聞アーカイブ 17年11月8日掲載 【工場ルポ】 日新製鋼・東予製造所(上)「ZAM」主力生産拠点/構内輸送を完全無人化
日新製鋼・東予製造所は、同社の鋼板製造プロセス技術を結集した普通鋼冷延鋼板の製造基地で、看板商品「ZAM」(高耐食溶融亜鉛・アルミ・マグネシウム合金めっき鋼板)の主力生産拠点。「年産180万トン規模で、酸洗・冷延、めっきラインともフル生産を続けている。安定操業を維持し、収益力を高めることが最大のテーマとなっている」(渡辺勉所長)。物流を完全無人化し、省エネも追求した高品質・高効率の最新鋭製造現場を取材した。

【地域に密着】
東予製造所は、瀬戸内海に面し、西日本最高峰の石鎚連峰に囲まれる自然豊かな愛媛県西条市にある。JR予讃線の壬生川駅から車で海岸線に向かうと5分ほどで芝生のグリーンベルトに囲まれた製造所が目の前に現れる。取材日は快晴で、「アルスター鋼板」(自社製品)で外装された工場建屋が銀色に輝いている。
敷地面積は約76万平方メートル(23万坪)。うち、約33万平方メートルを酸洗・冷延ライン、亜鉛めっきライン、事務所・厚生棟などに使用している。沿岸部にある約43万平方メートルの遊休地は大規模太陽光発電(23メガワット)用地として貸与している。
めっき工場のクーリングタワー屋上からは、全天候バースがある埠頭や「しまなみ海道」に連なる島々を眺めることができる。新居浜方面に目を移すと今治造船、住友重機械工業、アサヒビールなどの工場が並ぶインダストリアルパークを一望できる。
地元高校生のインターンシップを実施し、「えひめ国体」のオフィシャルサポーターを引き受けるなど地域密着型の活動を展開。社員104人、協力会社140人の244人体制。社員のうち現場は70人で4直3交替が主な勤務形態。「定期採用では地元の優秀な人材を確保できている。今後は女性社員の採用を増やしていく」(渡辺所長)方針である。
【所内輸送を無人化】
東予が製造するのは冷延鋼板とZAM、合金化溶融亜鉛めっき鋼板のペンタイト、ミニマイズド・スパングル処理を施したペンタイトB。
原板となるホットコイルは、呉製鉄所(広島県)から専航船(積載量1800トン×2隻)で瀬戸内海を約4時間で横断。バースに到着すると半自動クレーンによってパレット上に荷揚げされる。
すべての構内輸送をコンピューター制御し、完全無人化。5台の無人・無軌道搬送車「AGV」(積載量120トン、時速10キロ)がバースと工場をひっきりなしに往復している。AGVが原板を工場内に搬入し、製品をバースに搬出する。
屋内搬送、生産ラインへの母材投入、製品取り出しに使うクレーンもすべてコンピューター制御による完全無人化を実現。
燃料には排ガスがクリーンなLPガスを使用し、所内で使う全エネルギーをコンピューターで監視・制御。排水処理は高度濾過技術と排水口一本化による集中制御・監視を徹底している。

【酸洗・冷延ライン】
工場建屋は酸洗・冷延、ロールショップ、めっきの3棟が連結して並列する。
酸洗・冷延工場のメーン設備が全長330メートルのRSPM(酸洗・タンデム冷延ミル連結連続設備)。オペレーターは入側、出側、センター、検査など6人。
酸洗ラインは、国内唯一で、国内外特許を取得しているプレ圧延によるメカニカルデスケーラーを装備する。黒皮のホットコイルを上下から強圧下して表面の酸化物(スケール)に微細な割れ目を生じさせ、剥離し易い状態にしてブラシロールで除去。塩酸洗浄によるケミカルデスケールの効率を飛躍的に向上させ、酸洗槽を従来の2分の1に短縮し、酸液低温化による省エネ効果も発揮している。
冷延ラインは6―High・4タンデムで、ラインスピードは最速1500メートル/分。高圧下を得意とする小径ワークロールを採用。自動制御で板厚と形状をコントロールし、誤差数ミクロンの高精度圧延を実現。最厚7・5ミリの酸洗コイルを最薄0・15ミリまで圧延する。
【6ミリZAMを製造】
ロールショップ棟を横切り、めっき工場に入る。メーン設備は日新の表面処理鋼板製造プロセス技術を盛り込んだ全長380メートルのHCGL(高品質連続溶融亜鉛めっきライン)。6ミリまでの厚手ZAMをつくり込む高効率・高品質ラインである。
自動搬送ラインで運ばれてきた冷延コイルは、ライン中央にあるペイオフリールにセットされる。コイルを連続化するウエルダーは、薄ゲージ用のナローラップ溶接、厚ゲージ用のマグ溶接を使い分けている。
前処理槽で脱脂して油を完全に除去されたコイルは、予熱炉―竪型直火式還元炉―横型ラジアントチューブ炉の連続焼鈍プロセスに入る。ここで700―850度に加熱され、加工性を回復するとともに、めっきが付着し易い状態になる。厚物対応として、竪型直火式還元炉を採用していることが特徴である。コイルは冷却セクションを通過し、めっきセンターセクションへ向かう。
(谷藤 真澄)

【地域に密着】
東予製造所は、瀬戸内海に面し、西日本最高峰の石鎚連峰に囲まれる自然豊かな愛媛県西条市にある。JR予讃線の壬生川駅から車で海岸線に向かうと5分ほどで芝生のグリーンベルトに囲まれた製造所が目の前に現れる。取材日は快晴で、「アルスター鋼板」(自社製品)で外装された工場建屋が銀色に輝いている。
敷地面積は約76万平方メートル(23万坪)。うち、約33万平方メートルを酸洗・冷延ライン、亜鉛めっきライン、事務所・厚生棟などに使用している。沿岸部にある約43万平方メートルの遊休地は大規模太陽光発電(23メガワット)用地として貸与している。
めっき工場のクーリングタワー屋上からは、全天候バースがある埠頭や「しまなみ海道」に連なる島々を眺めることができる。新居浜方面に目を移すと今治造船、住友重機械工業、アサヒビールなどの工場が並ぶインダストリアルパークを一望できる。
地元高校生のインターンシップを実施し、「えひめ国体」のオフィシャルサポーターを引き受けるなど地域密着型の活動を展開。社員104人、協力会社140人の244人体制。社員のうち現場は70人で4直3交替が主な勤務形態。「定期採用では地元の優秀な人材を確保できている。今後は女性社員の採用を増やしていく」(渡辺所長)方針である。
【所内輸送を無人化】
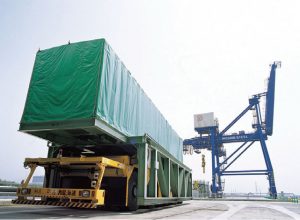
原板となるホットコイルは、呉製鉄所(広島県)から専航船(積載量1800トン×2隻)で瀬戸内海を約4時間で横断。バースに到着すると半自動クレーンによってパレット上に荷揚げされる。
すべての構内輸送をコンピューター制御し、完全無人化。5台の無人・無軌道搬送車「AGV」(積載量120トン、時速10キロ)がバースと工場をひっきりなしに往復している。AGVが原板を工場内に搬入し、製品をバースに搬出する。
屋内搬送、生産ラインへの母材投入、製品取り出しに使うクレーンもすべてコンピューター制御による完全無人化を実現。
燃料には排ガスがクリーンなLPガスを使用し、所内で使う全エネルギーをコンピューターで監視・制御。排水処理は高度濾過技術と排水口一本化による集中制御・監視を徹底している。

【酸洗・冷延ライン】
工場建屋は酸洗・冷延、ロールショップ、めっきの3棟が連結して並列する。
酸洗・冷延工場のメーン設備が全長330メートルのRSPM(酸洗・タンデム冷延ミル連結連続設備)。オペレーターは入側、出側、センター、検査など6人。
酸洗ラインは、国内唯一で、国内外特許を取得しているプレ圧延によるメカニカルデスケーラーを装備する。黒皮のホットコイルを上下から強圧下して表面の酸化物(スケール)に微細な割れ目を生じさせ、剥離し易い状態にしてブラシロールで除去。塩酸洗浄によるケミカルデスケールの効率を飛躍的に向上させ、酸洗槽を従来の2分の1に短縮し、酸液低温化による省エネ効果も発揮している。
冷延ラインは6―High・4タンデムで、ラインスピードは最速1500メートル/分。高圧下を得意とする小径ワークロールを採用。自動制御で板厚と形状をコントロールし、誤差数ミクロンの高精度圧延を実現。最厚7・5ミリの酸洗コイルを最薄0・15ミリまで圧延する。
【6ミリZAMを製造】
ロールショップ棟を横切り、めっき工場に入る。メーン設備は日新の表面処理鋼板製造プロセス技術を盛り込んだ全長380メートルのHCGL(高品質連続溶融亜鉛めっきライン)。6ミリまでの厚手ZAMをつくり込む高効率・高品質ラインである。
自動搬送ラインで運ばれてきた冷延コイルは、ライン中央にあるペイオフリールにセットされる。コイルを連続化するウエルダーは、薄ゲージ用のナローラップ溶接、厚ゲージ用のマグ溶接を使い分けている。
前処理槽で脱脂して油を完全に除去されたコイルは、予熱炉―竪型直火式還元炉―横型ラジアントチューブ炉の連続焼鈍プロセスに入る。ここで700―850度に加熱され、加工性を回復するとともに、めっきが付着し易い状態になる。厚物対応として、竪型直火式還元炉を採用していることが特徴である。コイルは冷却セクションを通過し、めっきセンターセクションへ向かう。
(谷藤 真澄)

スポンサーリンク